Vacuum Forming Machine
A Vacuum Forming Machine is a type of thermoforming machine used in manufacturing processes to create plastic parts and packaging by heating a sheet of plastic material until it becomes pliable and then forming it over a mold or pattern using vacuum pressure. This process is commonly used for producing items like blister packs, trays, containers, and various plastic parts.
Working process of Vacuum Forming Machine:
1. Heating: The process begins with a flat sheet of plastic material, typically made from materials like acrylic, PVC, PET, or polystyrene. This sheet is loaded into the vacuum forming machine. The heating element in the machine is used to heat the plastic sheet until it becomes soft and pliable. The temperature and heating time depend on the type and thickness of the plastic material being used.
2.Mold or Pattern: Underneath the plastic sheet, there is a mold or pattern that defines the shape of the final product. The mold can be made from various materials, including wood, aluminum, or machined metal, depending on the complexity and durability requirements of the product.
3.Vacuum Forming: Once the plastic sheet is heated and soft, it is lowered over the mold. A vacuum is then applied to the space between the mold and the plastic sheet. This vacuum removes the air, creating a pressure differential that forces the heated plastic sheet to conform tightly to the contours of the mold. The vacuum also helps to ensure uniform thickness throughout the formed part.
4. Cooling: After the plastic has taken the shape of the mold, it needs to cool and solidify. Some vacuum forming machines have built-in cooling systems, while others rely on ambient air or additional cooling equipment to expedite the cooling process. Cooling may take a few seconds to several minutes, depending on the material and thickness.
5. Trimming: Once the plastic has cooled and solidified, the excess material is trimmed away to reveal the final product. This can be done manually or using automated trimming equipment.
Vacuum forming offers several advantages, including relatively low tooling costs, fast cycle times, and the ability to produce large, lightweight, and durable parts. Vacuum Forming Machine is better suited for producing parts with simple to moderate complexity.
Advantages of Vacuum Forming Machine:
Vacuum forming machines offer several advantages across various industries due to their versatility and cost-effectiveness. Here are some of the key advantages of vacuum forming machines:
1. Cost-Efficiency: Vacuum forming is a cost-effective manufacturing process, especially for small to medium production runs. The molds used in vacuum forming are typically less expensive to produce compared to injection molds or other manufacturing methods.
2. Versatility: Vacuum forming can be used to create a wide range of products, from packaging materials to automotive components, signage, and consumer goods. It can accommodate various materials, including plastics like ABS, PVC, polystyrene, and more.
3. Quick Turnaround: Vacuum forming is a relatively fast process, making it suitable for rapid prototyping and production. Tooling setup is minimal, and parts can be produced quickly once the mold is ready.
4.Low Material Waste: Vacuum forming generates minimal material waste compared to other processes like CNC machining. Sheets of plastic are heated and formed to match the shape of the mold precisely, reducing excess material waste.
5.Design Flexibility: Vacuum forming allows for complex shapes and designs to be created, including undercuts and deep draws. It is suitable for producing parts with intricate details and textures.
6. Customization: Vacuum forming machines can be easily adjusted to accommodate changes in design or material. This flexibility is beneficial for manufacturers who need to produce variations of the same product.
7. Reduced Tooling Costs: While the initial mold creation can be an expense, it is generally more affordable than other tooling options like injection molds. This makes vacuum forming an attractive choice for small-scale production.
8. Low Maintenance: Vacuum forming machines are relatively simple in design and require minimal maintenance compared to some other manufacturing equipment.
9.Ease of Operation: Vacuum forming machines are relatively easy to operate, making them accessible to a wide range of users. Skilled operators can produce high-quality parts consistently.
10.Consistency: Vacuum forming provides consistent part quality when set up correctly, making it suitable for producing large quantities of identical parts.
11.Reduced Lead Times: Shorter tooling and setup times mean reduced lead times for production. This can be crucial in meeting tight project deadlines.
12.Energy Efficiency: Vacuum forming typically requires less energy compared to other manufacturing processes like injection molding, making it more environmentally friendly.
13.Wide Range of Materials: Vacuum forming can work with various materials, allowing manufacturers to choose materials that suit their specific requirements for strength, appearance, or other properties.
For many applications, Vacuum Forming Machine is an efficient and cost-effective choice for producing high-quality plastic parts.
Application Industries for Vacuum Forming Machine
Vacuum forming machines are versatile tools used in various industries for shaping plastic sheets into different forms and products. The process involves heating a thermoplastic sheet until it becomes pliable and then using a vacuum to mold it over a mold or pattern.
1. Packaging Industry: Vacuum forming is commonly used to create blister packaging for consumer goods, as well as clamshell packaging for electronic components, toys, and other products. It provides a clear and protective enclosure for the items.
2. Automotive Industry: Vacuum forming is used to create interior components like dashboards, door panels, and trim pieces. It's also used for exterior components like vehicle body panels and mud flaps.
3. Medical Industry: The medical field often uses vacuum forming for the production of custom-fitted orthopedic devices, dental trays, and medical packaging.
4. Aerospace Industry: Vacuum forming can be used for producing lightweight and durable components for aircraft interiors, such as overhead bins and interior panels.
5. Food Industry: Vacuum-formed trays and containers are used for food packaging and storage. They are known for their durability, cleanliness, and ability to showcase food products.
6. Display and Signage Industry: Vacuum-formed plastic sheets are used to create various types of signs, point-of-sale displays, and promotional materials.
7. Toy and Recreational Industry: Toys, games, and recreational equipment often use vacuum-formed plastic for components, including action figures, game board pieces, and protective gear.
8. Custom Manufacturing: Vacuum forming is employed in custom manufacturing processes to create one-off or limited-production parts for various industries. This includes prototype development and small-batch production.
9. Architectural and Construction: In architecture and construction, vacuum-formed plastic sheets are used for decorative wall panels, ceiling tiles, and other interior and exterior features.
10. Hobby and Craft: DIY enthusiasts and hobbyists use vacuum forming machines for various projects, from creating model parts to costume accessories.
11. Educational Sector: Vacuum forming is a valuable educational tool for teaching students about plastic manufacturing processes and design principles.
12. Art and Design: Artists and designers use vacuum forming to create unique sculptures, lampshades, and other creative pieces.
13. Marine Industry: Vacuum-formed parts are used in boats and marine equipment for their lightweight and corrosion-resistant properties.
14. Electronics Industry: Vacuum-formed plastic can be used to create casings and enclosures for electronic devices, such as remote controls and handheld devices.
15. Sports Equipment: Vacuum forming is utilized in the production of protective gear like helmets, knee pads, and sports equipment components.
16. Thermoforming Industry: Some companies specialize in vacuum forming services and produce a wide range of plastic products for various industries.
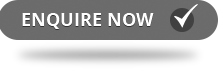